Quality Testing of Wire Bonds
DVS bulletin 2811 has been an integral part of testing wire bond contacts in microelectronics since 1996. It was originally initiated in the DVS working group AG2.4 “Bonding” by Dr. Rudolf (formerly TU Dresden) and Prof. Lang (formerly Fraunhofer IZM Berlin) and revised in February 2017 under the coordination of Bond-IQ GmbH. Due to ever-increasing requirements for electronic assemblies and new technologies, a further update is now necessary.
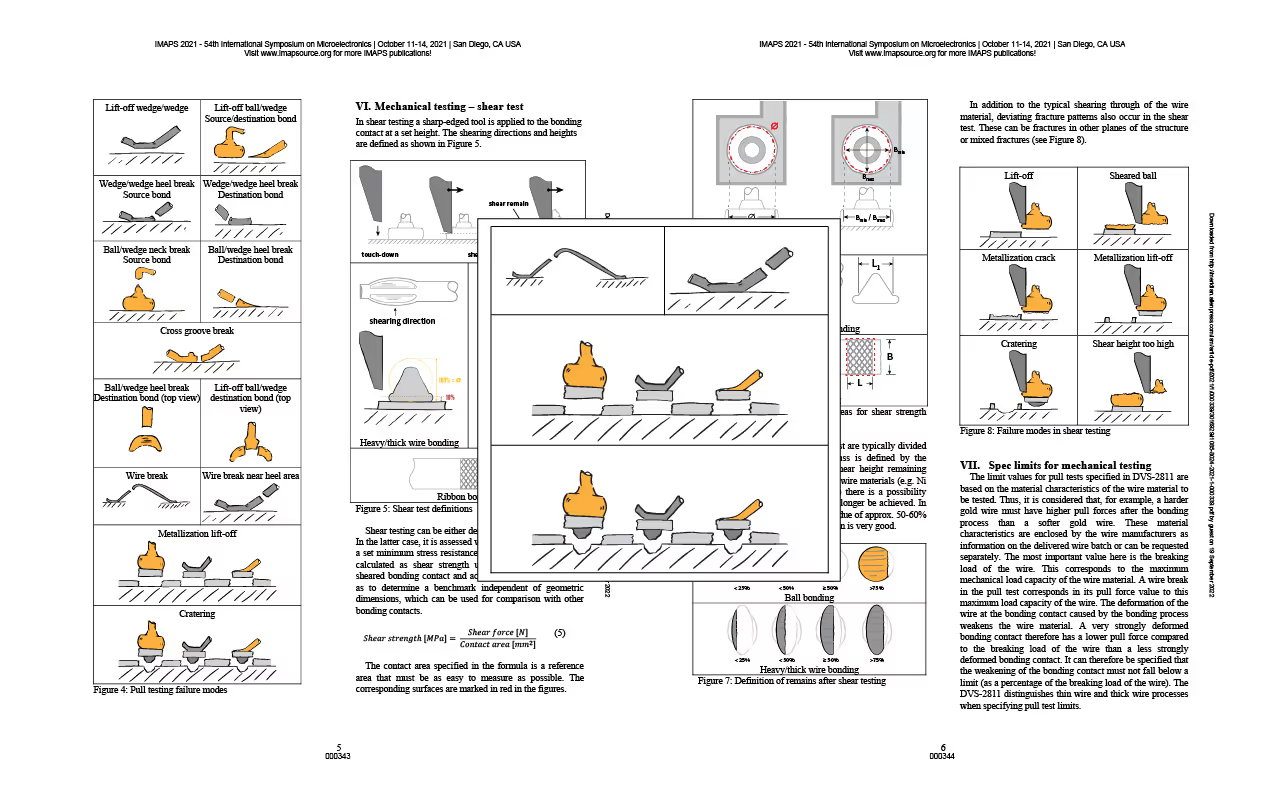
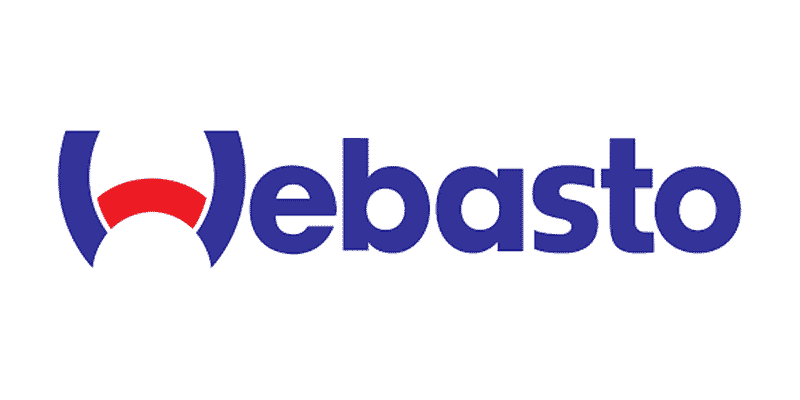
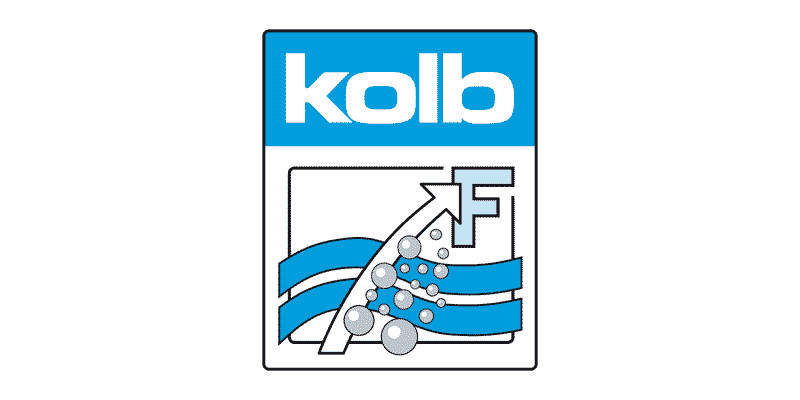

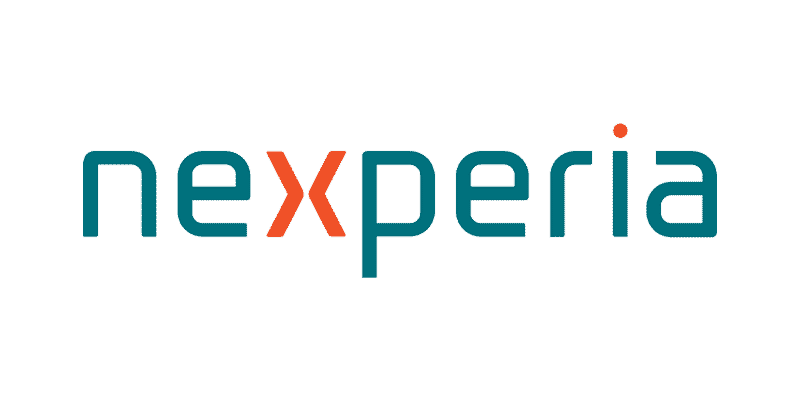
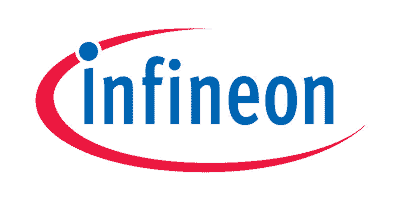
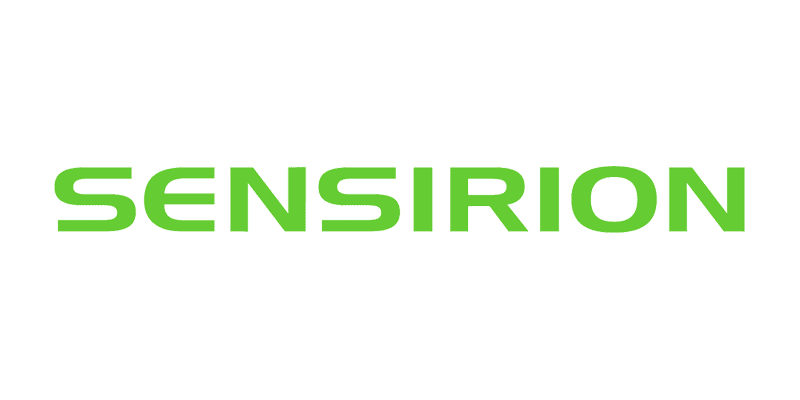
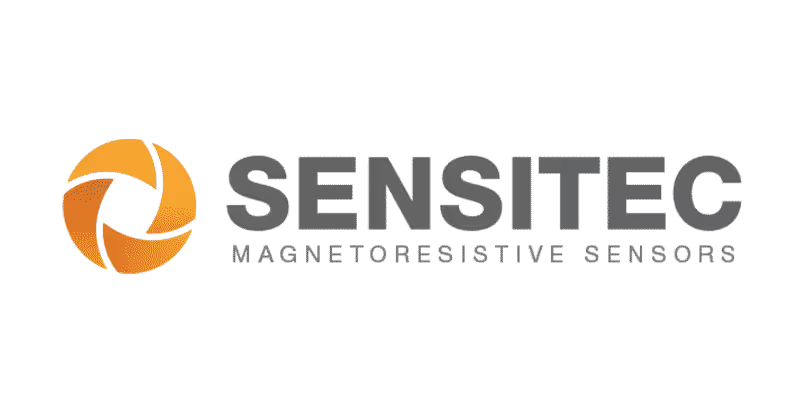
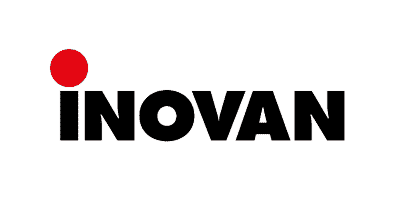
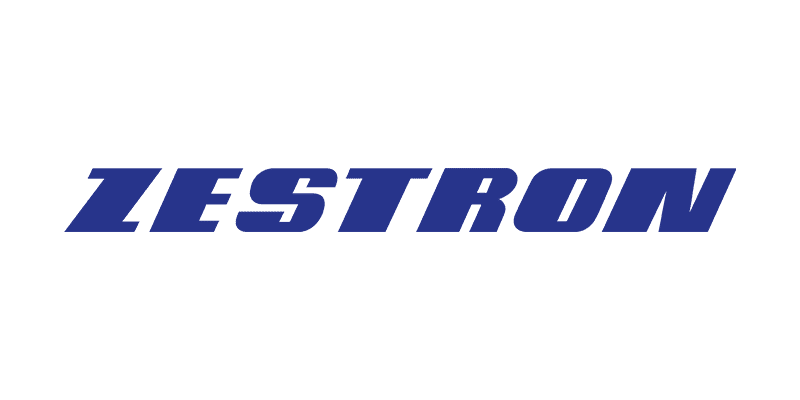
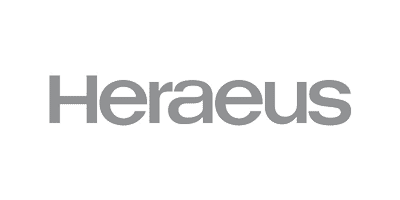
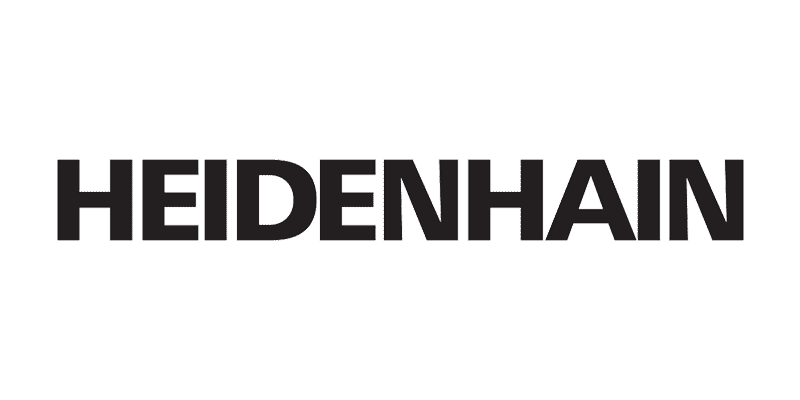
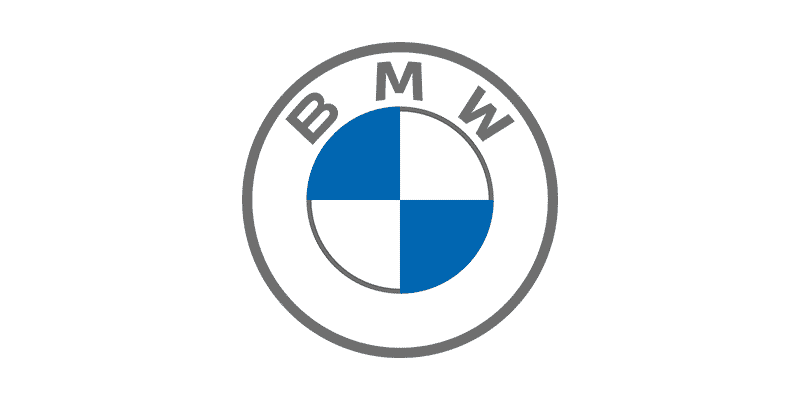
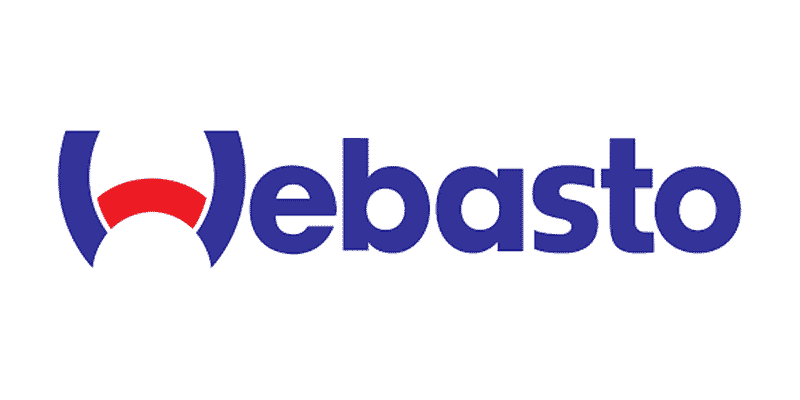
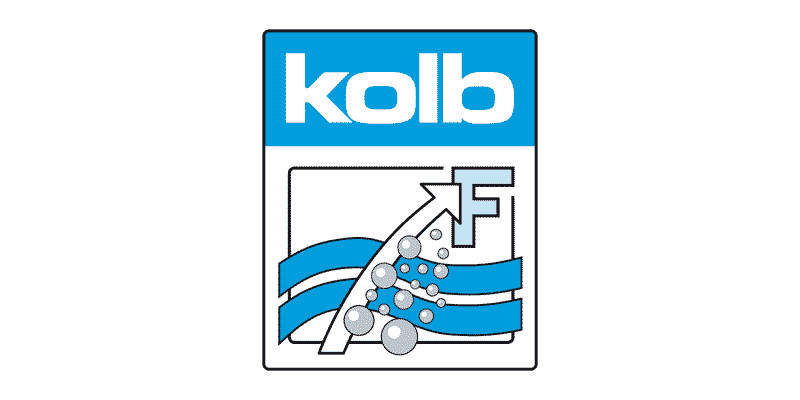

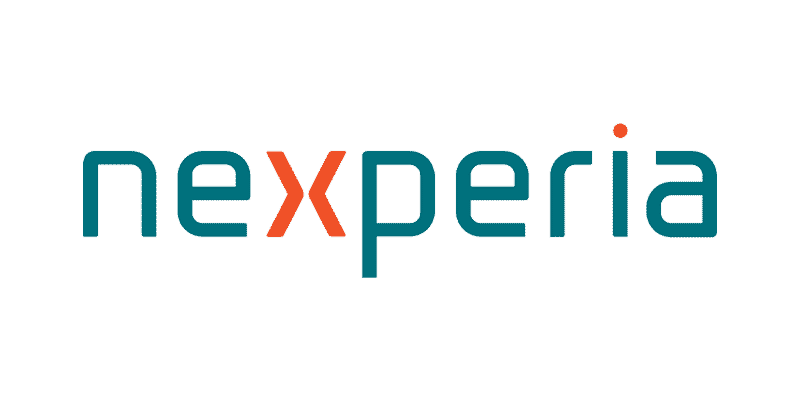
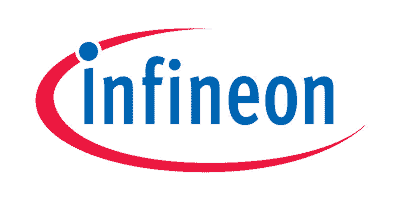
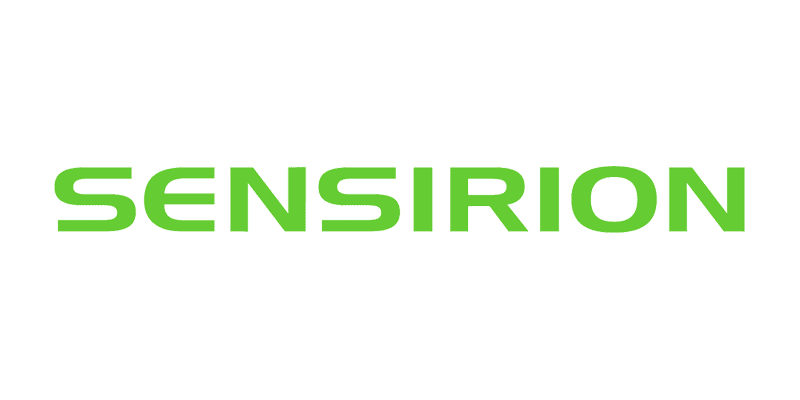
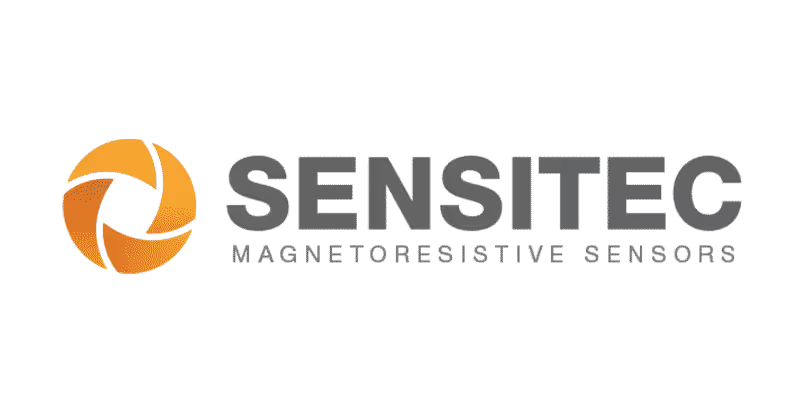
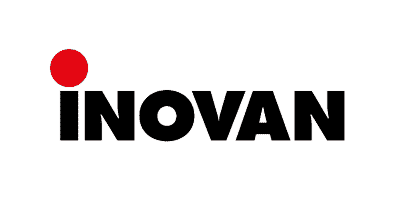
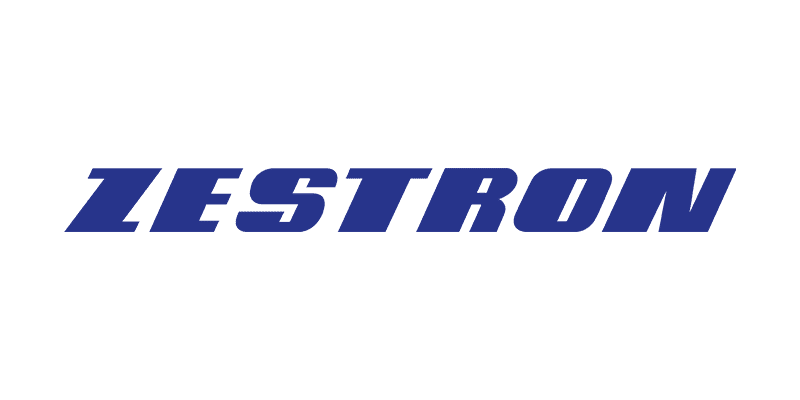
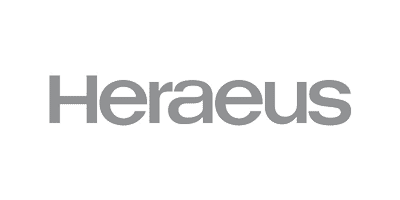
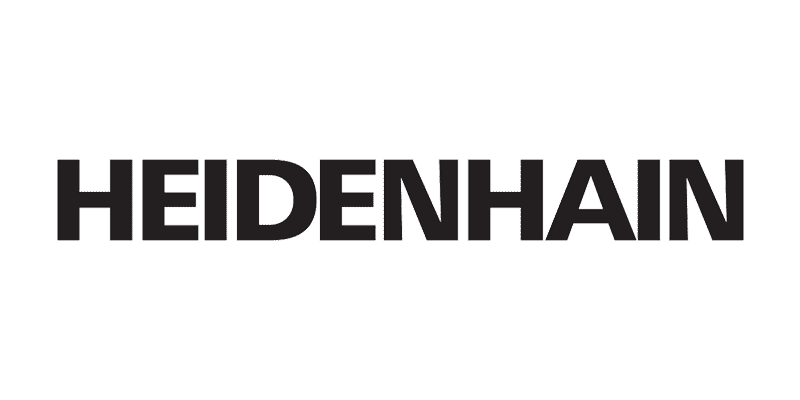
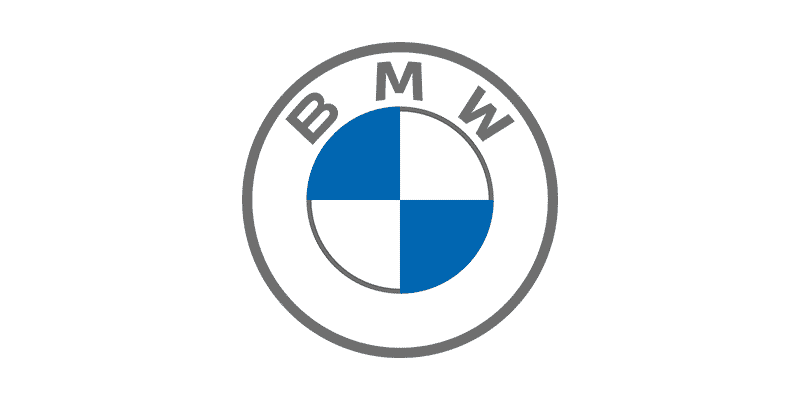
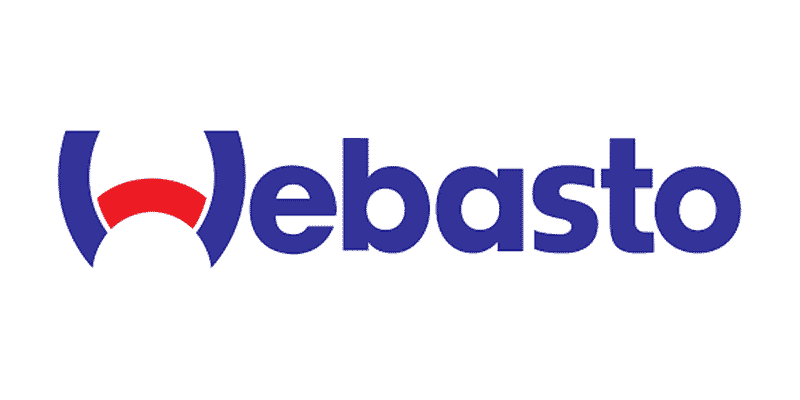
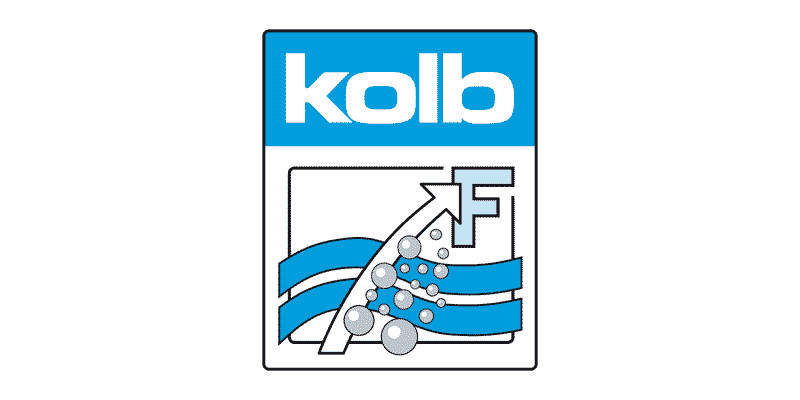

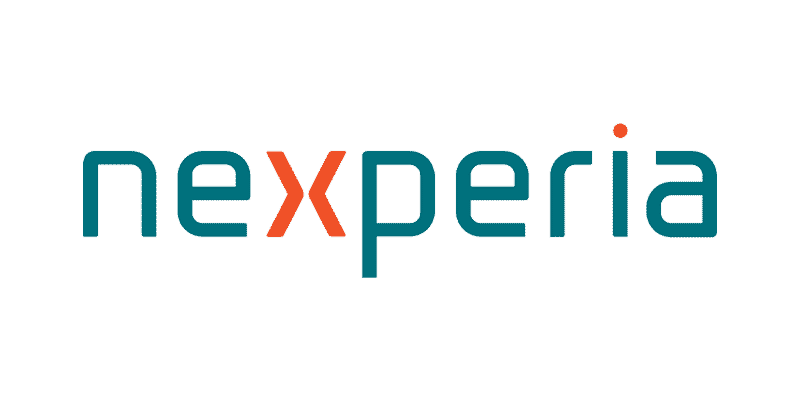
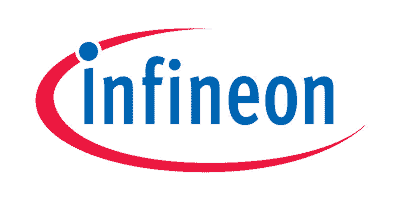
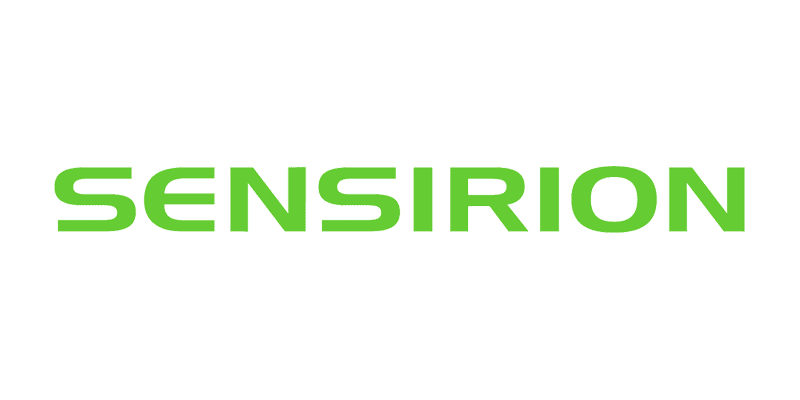
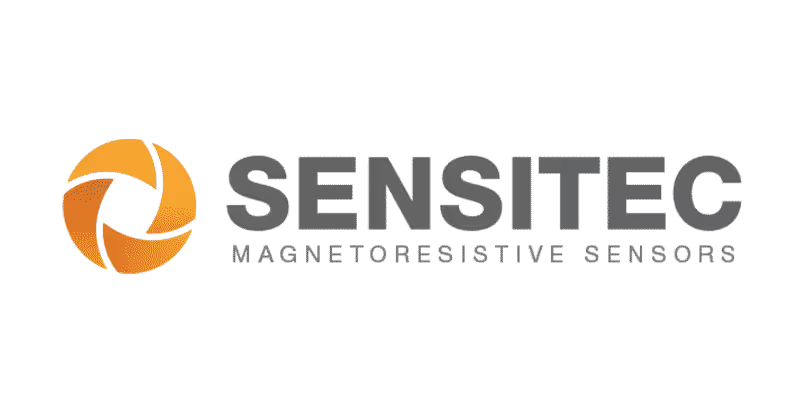
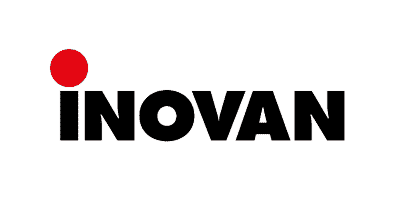
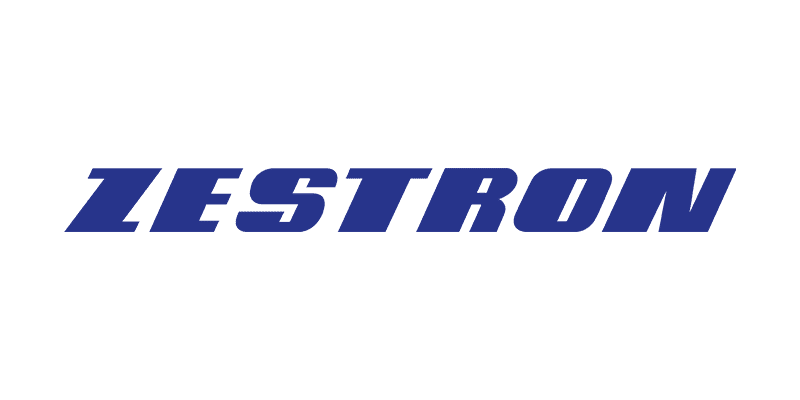
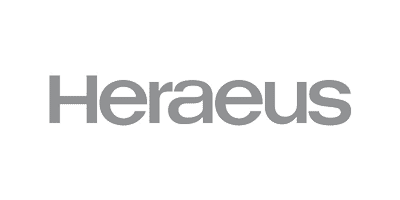
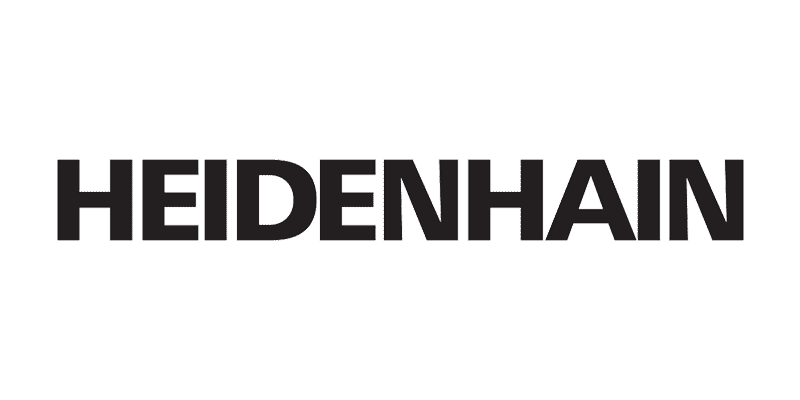
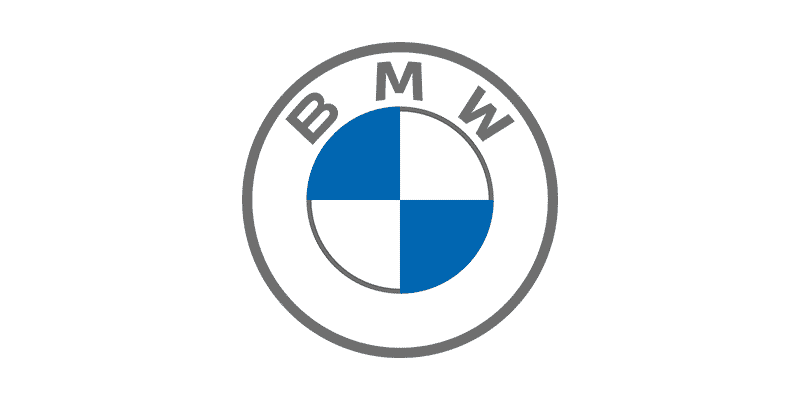
A look back in history of wire bond testing
The testing of wire bond contacts is a central component of quality control in the semiconductor industry. It has developed from simple visual inspections to highly specialized, standardized procedures that now cover mechanical, electrical, and visual aspects of bond quality.
In the early years, quality control was limited to visual inspections and simple mechanical tests. With the advent of pull testing in the 1960s, the first systematic method for evaluating the strength of a wire bonded connection was developed. In pull testing, a hook is placed under the wire and pulled in the z-direction until the connection breaks (destructive) or a defined force is reached (non-destructive).
Current requirements for testing wire bonds
In recent years, the range of materials used has expanded significantly: In addition to classic gold wires, silver, gold-coated silver, copper, palladium-coated (PCC) and gold-coated (PCC+Au) copper wires are now increasingly being used.
Bi-metal materials, such as aluminum-clad copper wire or single-sided aluminum-coated ribbons, are also gaining in importance. The increased use of thick copper wire for power electronics requires an adaptation of testing methods, as copper has different mechanical properties to aluminum, which is the most commonly used material. At the same time, the demands on the interpretation of fracture patterns are increasing, as the variety of materials leads to more complex fracture mechanisms.
Higher reliability requirements, especially in safety-critical applications, make improved knowledge of the connection quality and the formation of interfaces essential. Last but not least, new testing methods developed for these modern materials and structures must be described and standardized in DVS 2811 to ensure uniform and reliable quality assessment.
Recent Publications
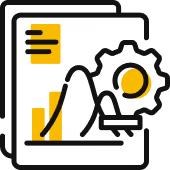
Mathematical considerations on pull tests and errors in formulas, some of which have been used in testing standards for a very long time.
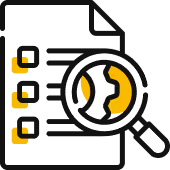
A combined method for analyzing the interface of thick wire bonds was presented at the IMAPS Conference 2021. The combination of BAMFIT and 3D fracture surface measurement enables a more precise evaluation of the bond quality. In addition to the shear test, the bonded area is measured directly. Four wire types were investigated using DoE to compare process windows and bond behavior.
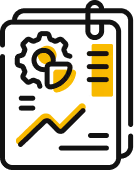
A revised version of the JEDEC standard for pull tests was published in September 2024.
Update activity 2025
Separation of Production and Process Development
In the first version of DVS 2811, a distinction was made between laboratory and production quality assessment. This distinction was abandoned in the 2017 update. However, it has become apparent that the very strict criteria of DVS 2811 are not suitable for all products and applications. Furthermore, the criteria are insufficient for very complex processes.
In order to gain flexibility here, a chapter will deal with testing in typical production processes. This chapter will describe the common test methods in such a way that they can be applied easily and pragmatically.
For testing within the scope of process optimization or qualification and certification, more detailed tests are described and recommendations for advanced strategies are given.
Visual and mechanical test of thin and thick wire bonds
As with previous versions, the update to DVS 2811 ensures that all specified characteristic values and limit values for mechanical tests are material-dependent. For example, different pull forces are required for soft wires than for hard wires. The influence of the geometry of wires and contacts is always factored out. Limit values are therefore specified in terms of strength rather than force in order to simplify comparison of the connection quality of different wire diameters.
Destructive and non-destructive test methods are listed separately. The applicability and benefits of non-destructive methods are discussed in order to provide users with even better guidance.
The evaluation criteria and limit values are based on existing standards such as MIL-STD-883, ASTM, and JEDEC. The aim of DVS 2811 is to meet at least the requirements of all other standards and to apply stricter test criteria where necessary.
That's what we've set out to do...
There are a few changes coming that'll make sure the DVS bulletin 2811 gets even more popular and accepted by users and industries.
- Improvement of the clarity of text passages and the structure of the document
- Streamlining of access to content and the ease of use
- Enhancement of image examples and illustrations
- Inclusion of microscope images to supplement schematic drawings
- Broader use of material-dependent characteristic values and limit values for pull and shear tests
- Expansion of existing chapters on thick wire and thick ribbon bonding with information on the processing of copper materials
- New chapters on the processing of particularly large material cross-sections
- Strengthening visibility among European and international companies
How to participate
A testing standard is only as good as its content, its relevance, its clarity and how practical it is in application. Progress in revising DVS bulletin 2811 depends on the participation, experience and input of all those involved. Wire bonding is experience. Experience that should be documented.
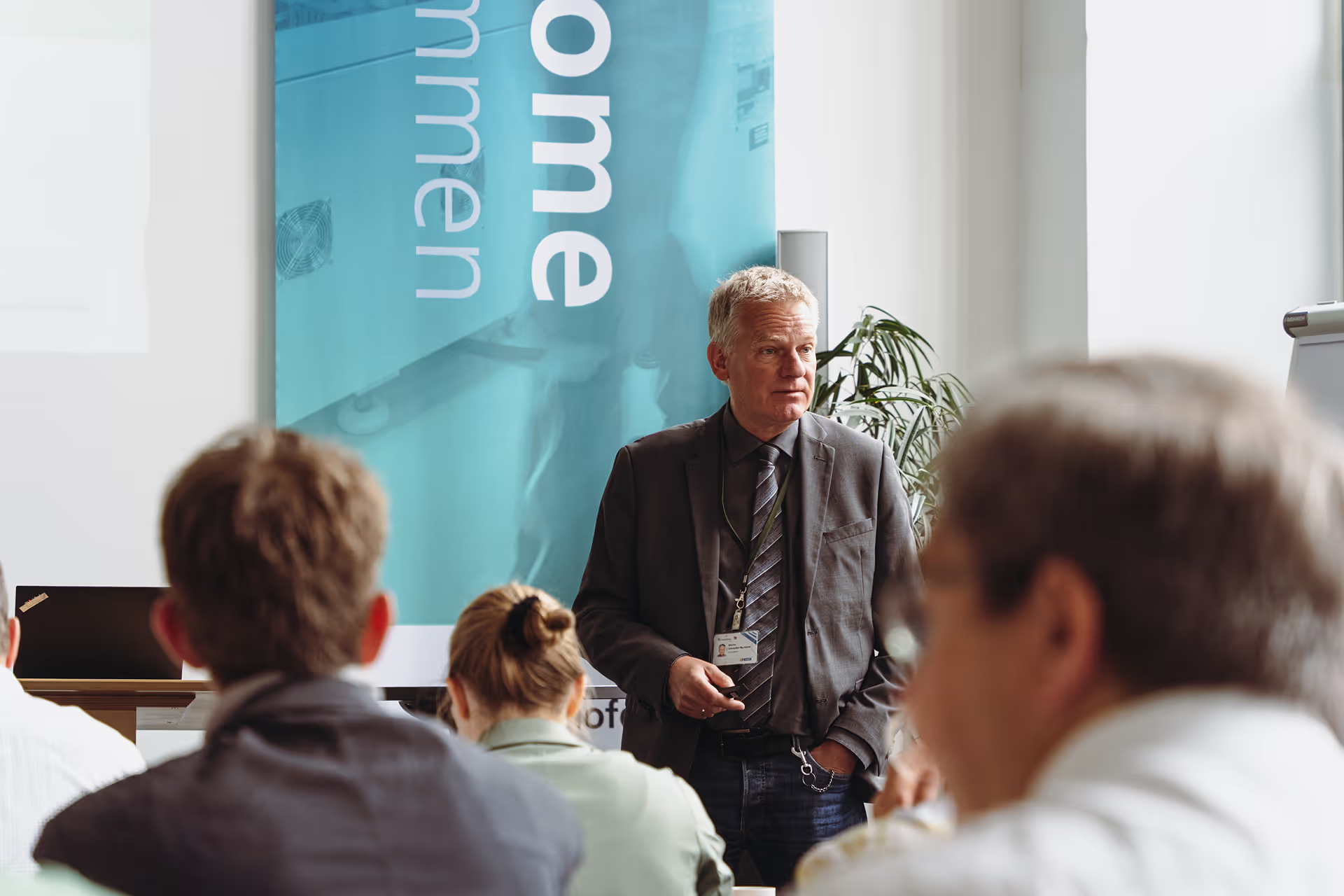
Latest News
At the 73rd meeting of the AG-Bonden (LINK), some of the participants got together and developed initial ideas for revising the DVS bulleting 2811. All participants consider it particularly important to improve the applicability and comprehensibility of the sheet, enhance illustrations and image examples, better integrate Cu thick wire and ribbon, include particularly large cross-sections, and strengthen European and international visibility.
All progress made in revising the DVS bulletin 2811 will be communicated at the online roundtable on wire bonding technology (LINK) in order to attract interested parties to participate. The project was presented on June 23.
In summer 2025, all participants will meet online via MS Teams for an initial meeting. Bond-IQ will coordinate the meetings and structure the content. The collaboration will take place using shared documents, so that revisions can be made quickly and efficiently without email ping-pong.