Investigating the Effects of Metallization Thickness on Kirkendall Voiding in Au Ball Bonds at High Temperatures
Title: Kirkendall voiding in Au ball bond interconnects on Al chip metallization in the temperature range from 100 – 200°c after optimized intermetallic coverage
Authors: M. Schneider-Ramelow; S. Schmitz; B. Schuch; W. Grübl
Dage 4000 (for pull tests)
XYZTec (for shear testing)
Wire types:3N pure Radix Plus2N plus 1% Pd HA34N pure AW99
20 tests per combination
Shear tests
Cross-sectional microstructuralanalysis
Cross-sectional analysis of intermetallic phase growth
Published: 2009
12 figures including pull and shear test results
5 tables summarizing lift-offs and force measurements
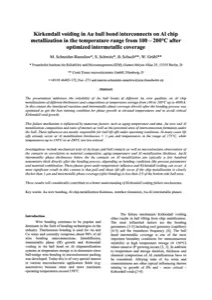
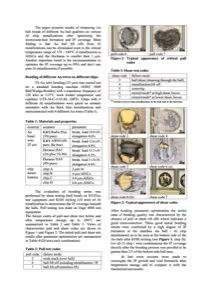
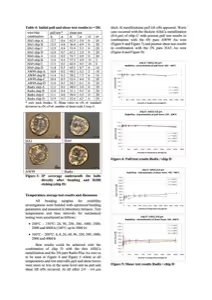

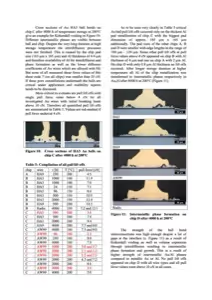
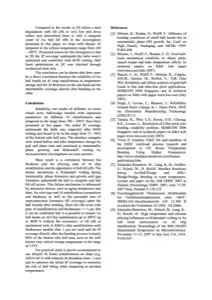
Executive Summary
This study examines a particular phenomenon known as Kirkendall voiding, which occurs at the interface between gold (Au) wires and aluminum (Al) metallization on chips. The primary objective is to ascertain the manner in which this voiding results in bond failure, particularly at elevated temperatures (100°C to 200°C), and to determine the influence of diverse materials on the dependability of the bonds.
The researchers tested a variety of combinations of Au wires and Al metallization on chips. They discovered that specific conditions, such as the thickness of the Al layer and its chemical composition, have a considerable impact on bond reliability. The use of thinner Al layers and optimized bonding conditions has been shown to prevent bond lift-offs, a common failure mechanism in these environments. The study recommends the use of Al alloys with reduced thickness to enhance long-term reliability in high-temperature applications.
Get your article summary
The summary will be sent to your email address
Main Focus
This study examines the phenomenon of Kirkendall voiding in Au ball bonds on Al chip metallizations at elevated temperatures (100–200°C). Specifically, this study examines the reliability of Au ball bonds under various conditions, with a particular focus on the influence of metallization thickness and intermetallic phase (IP) coverage on bond strength and failure mechanisms, particularly ball lift-off during extended temperature storage.
Background and Motivation
Wire bonding, particularly thermosonic Au bonding, continues to be a predominant interconnect technology in microelectronics due to its reliability and pervasive deployment in critical applications such as automotive electronics, where operating temperatures frequently exceed 150°C. Nevertheless, the growth of intermetallic phases between gold and aluminum under thermal stress can result in Kirkendall voiding, a significant reliability concern that may lead to ball bond lift-offs and mechanical failure.
The objective of this research is to investigate the influence of varying metallization thicknesses and compositions, particularly pure aluminum versus AlSiCu alloys, on the formation and growth of intermetallic phases and the occurrence of Kirkendall voids. The objective is to refine wire bonding techniques in order to enhance bond reliability at elevated temperatures, thereby preventing premature failure in industrial applications.
Methodology
The methodology of this study involved an in-depth investigation of the reliability of Au ball bonds on Al chip metallizations, with a focus on the influence of metallization thickness and intermetallic phase (IP) coverage on bond integrity. The experimental work began with the wire bonding process, where thermosonic Au wire bonding was performed using an ESEC 3088 Ball/Wedge Bonder, operating at a workholder temperature of 125°C and a transducer frequency of 120 kHz. A UTS-38-C-1/16-XL (SPT) capillary was used for bonding.
Four different Au wire types were used, including 3N pure Radix Plus, 4N pure K&S AW99, 2N plus 1% Pd Heraeus HA3, and 4N pure Heraeus HA9. These wires were bonded to chips with different Al metallization types and thicknesses. The metallization samples included pure Al with a thickness of 2 µm and AlSiCu alloys with thicknesses of 0.8 µm, 4 µm, and 4.4 µm. Each chip/wire combination was subjected to mechanical and microstructural tests to evaluate bond reliability and failure mechanisms.
The primary tests performed included pull and shear tests to evaluate the mechanical integrity of the bonds. Pull tests were performed using Dage 4000 equipment, while shear tests were performed using XYZTec equipment. The intermetallic phase coverage beneath the Au bead bonds was analyzed after 10 minutes of KOH etching of the Al metallization, allowing a detailed assessment of the extent of IP coverage immediately after the bonding process.
To evaluate the effects of thermal aging, the bonded samples were subjected to temperature storage at a range of temperatures between 100°C and 200°C, with storage times ranging from 24 hours to 4000 hours. Periodic mechanical tests were performed at intervals throughout the aging process to track changes in bond strength. In addition, cross-sectional analysis of the samples was performed after aging to examine the growth of intermetallic phases and the formation of Kirkendall voids. This combination of mechanical testing, intermetallic coverage analysis, and cross-sectional microstructural observations provided a comprehensive understanding of the effect of metallization thickness and bonding conditions on the occurrence of bond lift-off and the overall reliability of Au-Al joints under prolonged thermal stress.
Key Findings
- Intermetallic Phase Coverage: The study demonstrated that a minimum IP coverage of two-thirds beneath the Au ball is critical to prevent bond lift-offs. The optimal results were obtained when the IP coverage was approximately 90% of the bond area, particularly when thinner AlSiCu metallization was utilized (≤1 µm).
- Effect of Al Thickness: The thick Al metallizations (>1 µm), particularly the 4.4 µm AlSiCu sample, demonstrated the highest rate of failure (ball lift-offs). In contrast, the thinner metallization (0.8 µm AlSiCu) demonstrated the ability to maintain bond integrity even after prolonged exposure to high temperatures (up to 4,000 hours at 200°C).
- Temperature Sensitivity: The failure mechanisms, primarily pull and shear lift-offs, were found to be significantly accelerated at temperatures exceeding 160°C. The 4.4 µm AlSiCu sample exhibited the most severe deterioration, with pull forces reaching critical values (less than 4 cN) after 1,000 hours of storage at 200°C.
- Void Formation and Mechanical Strength: Notwithstanding the substantial void formation in thicker Al layers, the mechanical integrity of the interconnect was maintained due to the robust nature of the intermetallic phases (Au4Al). However, the formation of voids was found to be significantly correlated with bond failures, particularly in thicker aluminum metallizations.
Implications for Future Research and Industry
- Material Optimization: The findings indicate that AlSiCu metallizations, particularly those with thicknesses below 1 µm, are optimal for high-reliability applications. The combination of these materials with optimized IP coverage (up to 90%) can significantly reduce the risk of Kirkendall voiding and bond lift-offs, even under prolonged high-temperature conditions.
- Future Directions in Metallization Research: Further investigation into alternative alloy compositions and their impact on void formation may yield additional strategies to enhance bond reliability. Similarly, an investigation into alternative wire materials or coating techniques that impede interdiffusion between Au and Al could prove beneficial in the mitigation of Kirkendall voiding.
- Industrial Application: These findings are of paramount importance to industries that operate under high-temperature conditions, such as the automotive and aerospace electronics sectors. The incorporation of thinner AlSiCu metallizations and the assurance of optimal intermetallic phase coverage enable manufacturers to augment the durability and reliability of their wire bonds.
Limitations
- Metallization Types: The present study was confined to four distinct metallization types (pure Al and AlSiCu) and concentrated on a particular range of thicknesses (0.8 to 4.4 µm). Further research could extend the range of metallization compositions and investigate additional thickness levels to substantiate these findings more comprehensively.
- Long-Term Exposure: Although the study encompassed 4,000 hours of temperature aging, it is possible that real-world applications may necessitate the implementation of a more extensive testing period to ensure the comprehensive assessment of long-term reliability in harsh environments.
- Mechanical Testing: While pull and shear tests were employed to gauge bond strength, additional testing methods, such as fatigue or vibration testing, may offer more profound insights into the mechanisms underlying bond failure under real-world operating conditions. These limitations offer avenues for further investigation and improvement in future research endeavors.
Get your article summary
The summary will be sent to your email address